Private project
2022
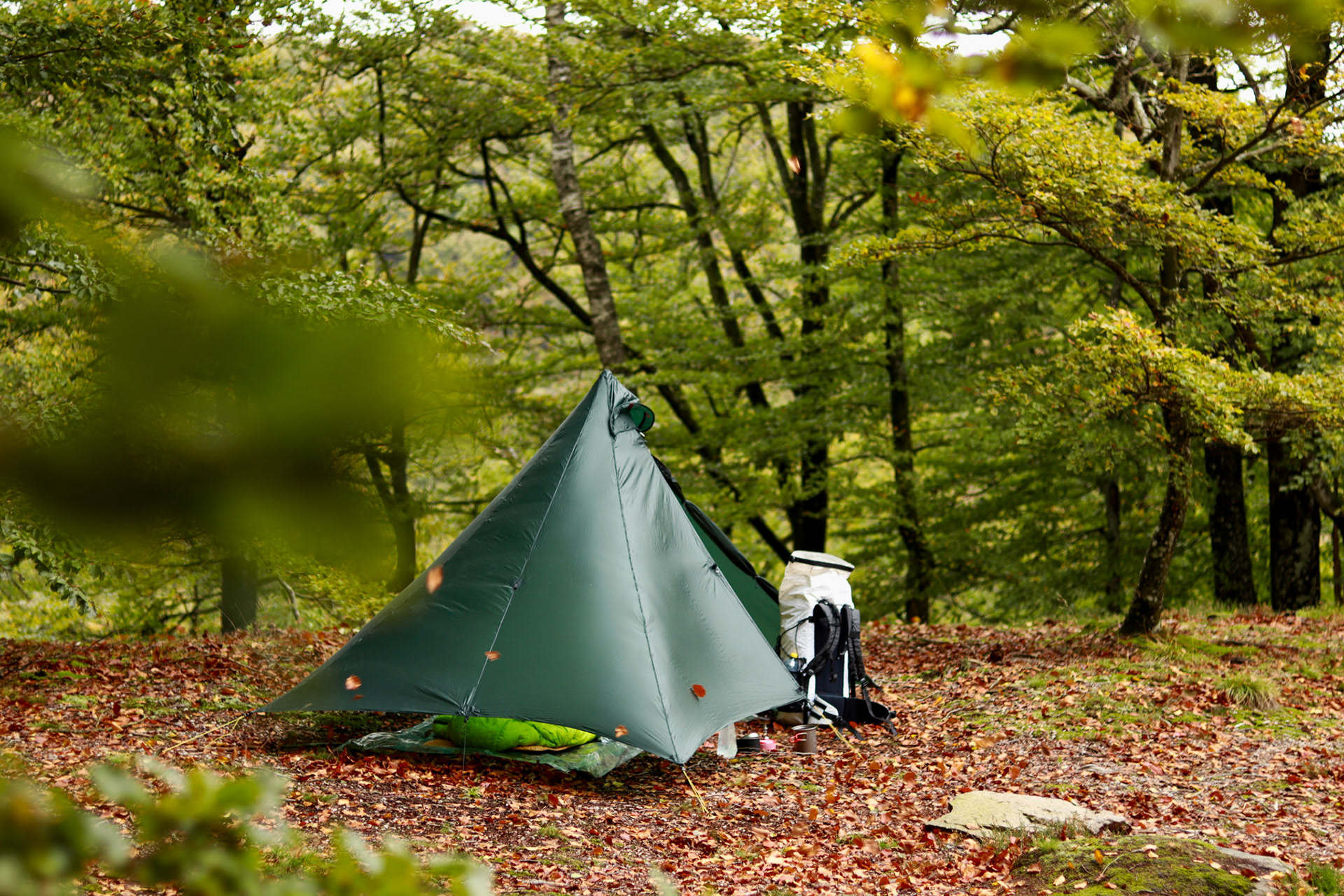
Need
This project originated in my own need for a new tent. I did already own a Hilleberg Nallo 3 and was very satisfied with it for two people but I felt that it was a bit too heavy for solo use. Therefor I wanted to create my own flexible solution that I wanted to be light enough for solo use, occasionally be used by two people and still handle tough weather conditions. It would preferably be a double-wall tent to better inhibit condensation.
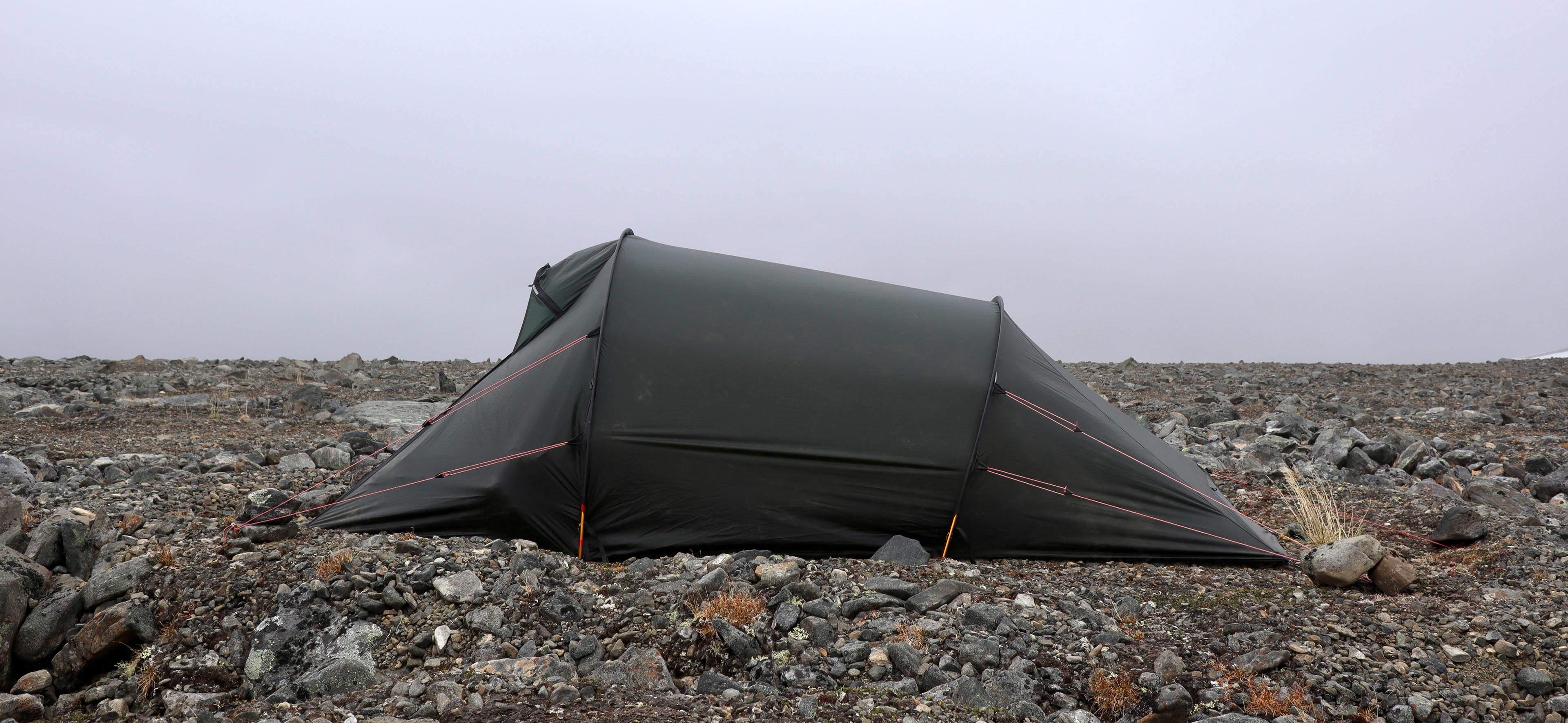
Current tent used for hiking in northern Sweden, Hilleberg Nallo 3 at 2,7kg.
Stable and comfortable, but not the lightest.
Stable and comfortable, but not the lightest.
Goals & Restrictions
I set up a collection of what goals and restrictions I had to make the tent a reality. The goals were a total weight of 1 kg (for both inner tent and outer fly), easy to pitch, waterproof, stable in wind and should be able to be pitched fly first. It should have the possibility to comfortable house two people even though it will primarily be a one-person tent.
My plan was to sew it myself and therefor the restrictions I had originated mostly in my own ability to sew and the materials that I were to use. I used Sil-Nylon fabric, which I had used for other projects before and had some prior experience both for how difficult it is to sew in, as well as how it stretches under load. Even though I see myself as a capable hobby seamstress, complex shapes in Sil-Nylon is significant difficulty to both sew and produce patterns for.
Material
I chose to use the Sil-Nylon fabric from Hilleberg as the main outer fabric. It is the same type that Hilleberg uses in their winter tents. This was both because it is a strong and qualitative fabric that is well suited for this purpose and because it is easily and cheaply available as spare material from Hilleberg themselves.
Other materials that could have been used is Dyneema-composite fabrics. This could have been a good choice as it is a more or less inelastic fabric with an amazingly strong fibers. This would remove the need of the so called ”cat-cuts” that Sil-Nylon needs to remedy it’s inherent stretch. Dyneema was ultimately not chosen because it’s exceedingly high cost per running meter of fabric and difficulty of processing.
Sketching
To explore multiple ideas and shapes I did a large number of rough sketches. Some shapes were inherently more interesting than others as I tried to maximize usable space, ease of production and wind resistance.
I had far-going ideas of combining elements of both tunnel tents and ridge tents. The front would look like a tunnel tent and benefit from the good wind-stable properties of such. The rear would take on the character of a ridge tent to save on weight and additional vertical height.
Ultimately I saw the use of trekking-poles as the main pole structure to be the best suitable solution to lower the carried weight. This would provide a double use for the trekking-poles but using only straight poles limits the possible shapes.
This led me to become more interested in pyramid-shaped tents to be an even better alternative. The somewhat symmetrical shape together with the slanted walls would render the shape handle wind well as well as being more or less sensitive to wind direction, providing more flexibility in where to pitch the tent. Also, if one trekking-pole would brake during the trip, there is only need for one to pitch the tent.
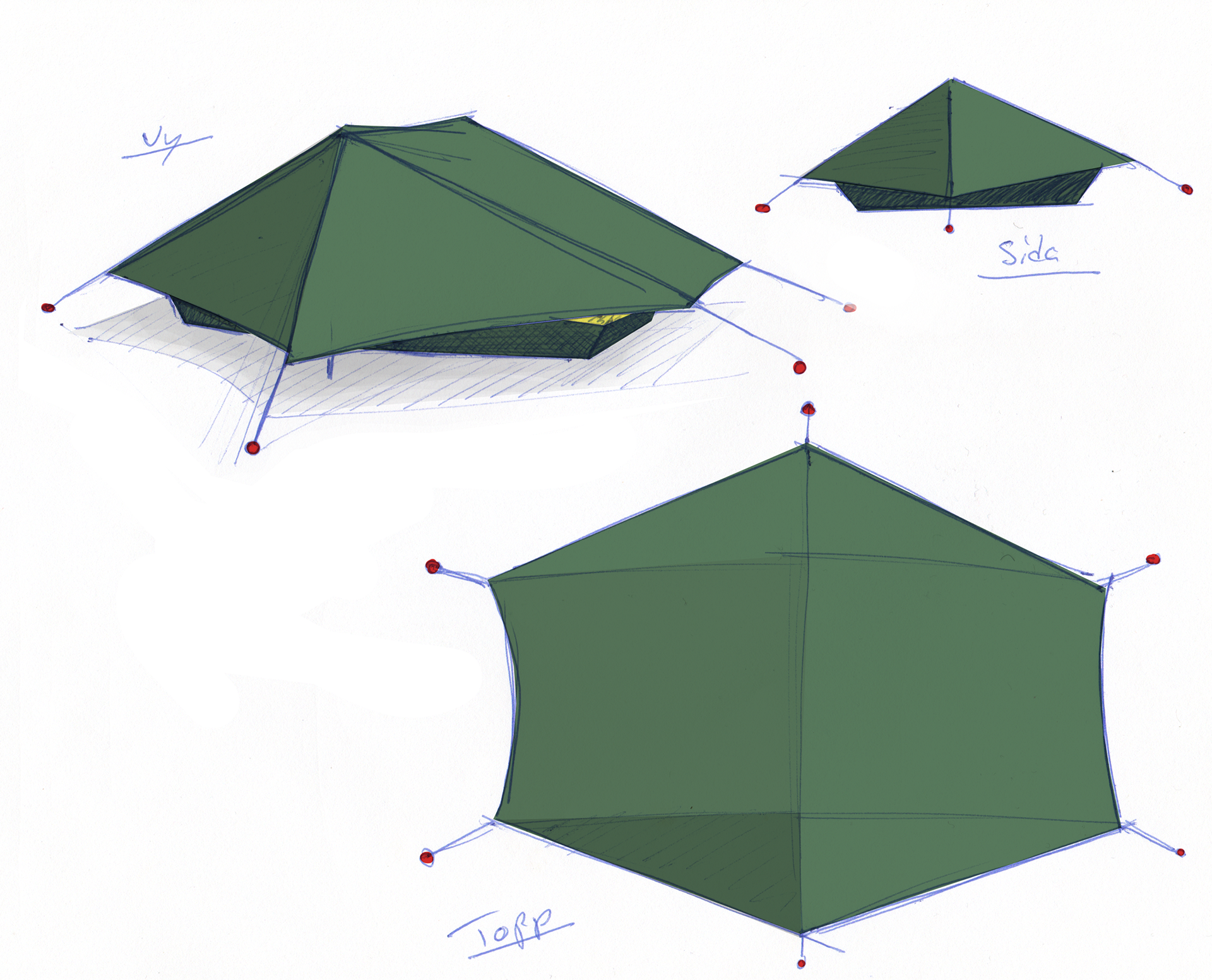
Early concept using to trekking poles. Provides a lot of headroom but could be less stable in wind.
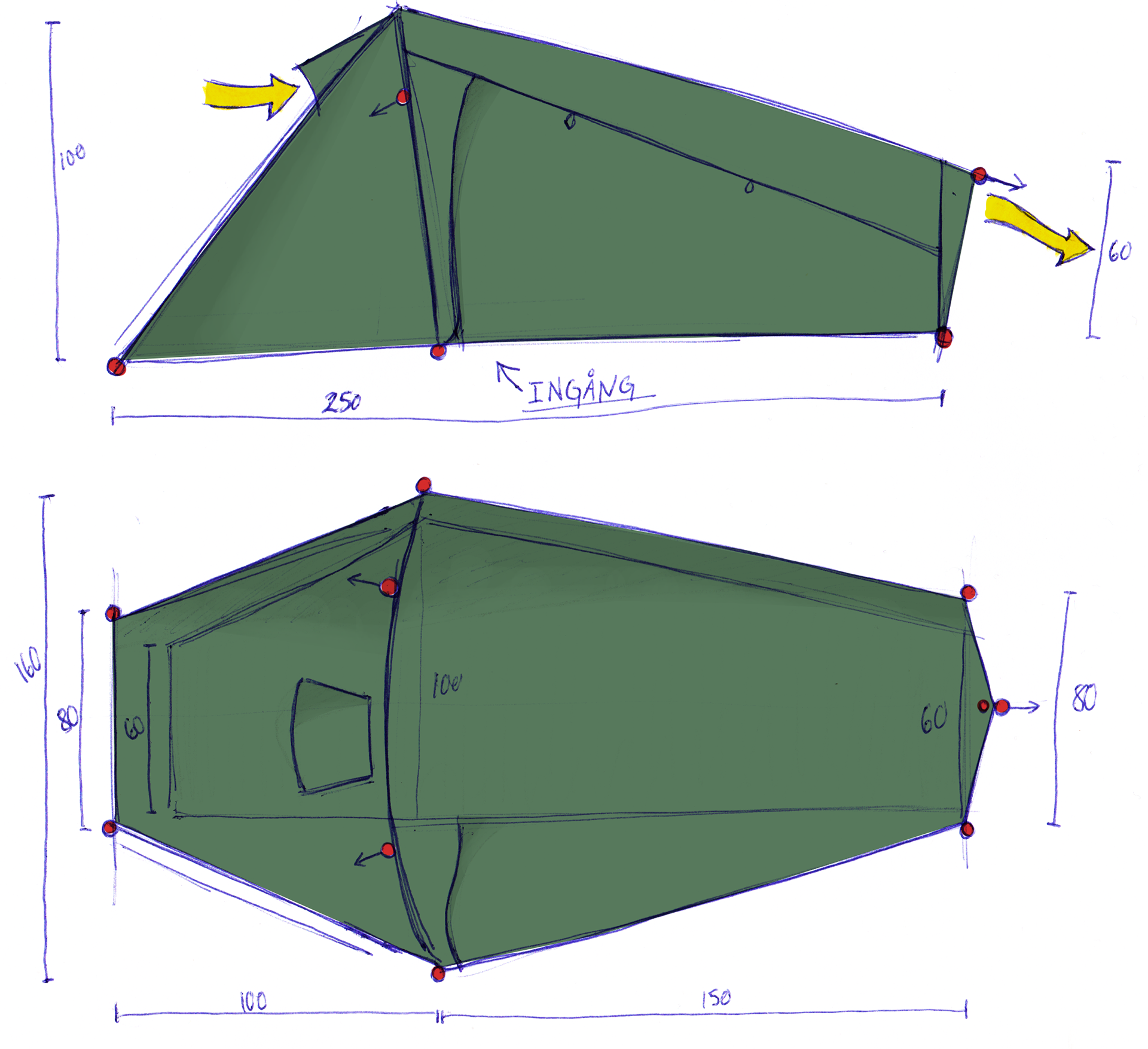
Concept combining elements from both tunnel and ridge tents
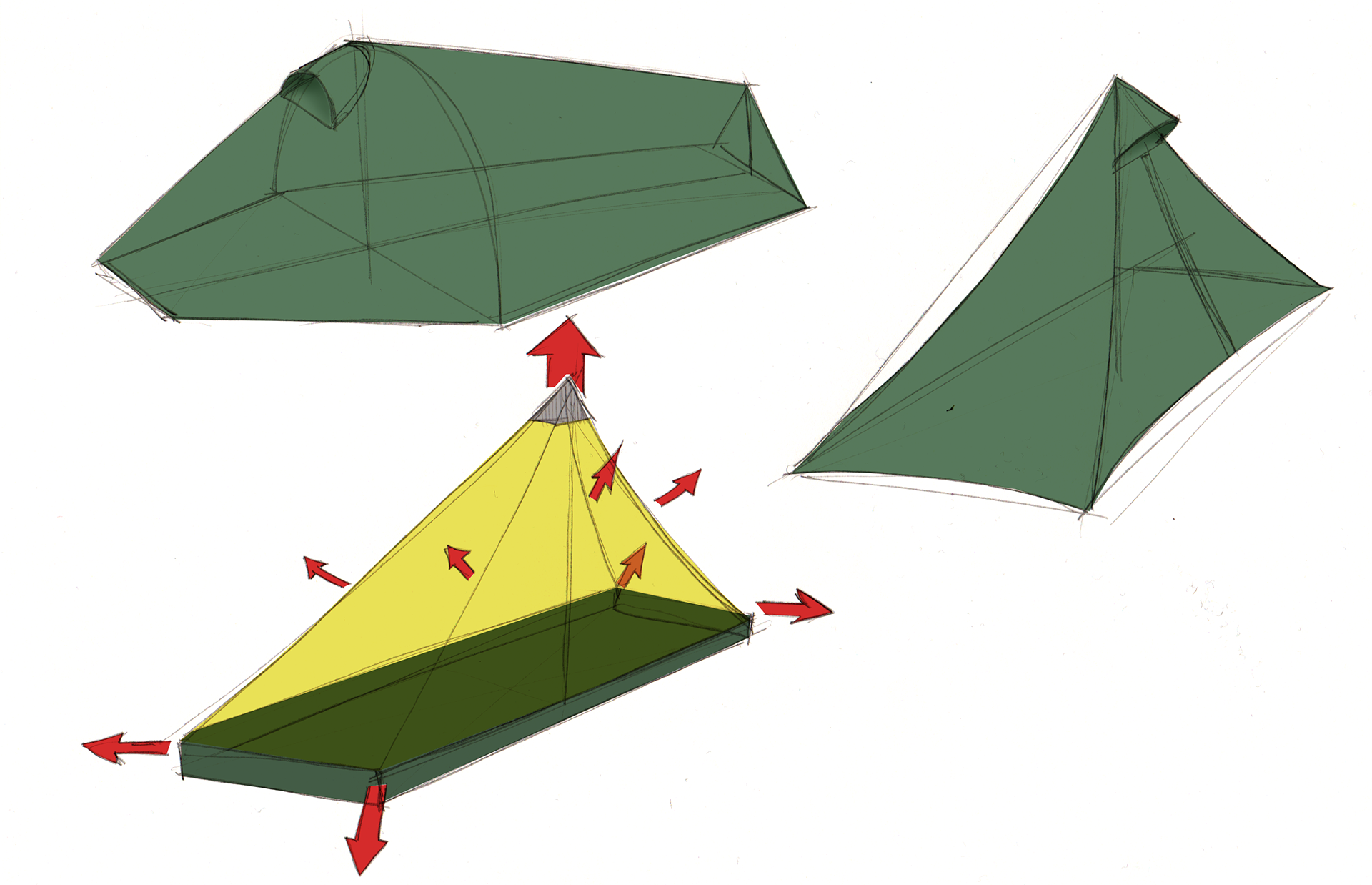
The development of the pyramid shape and how the inner tent would be connected to the outer fly.
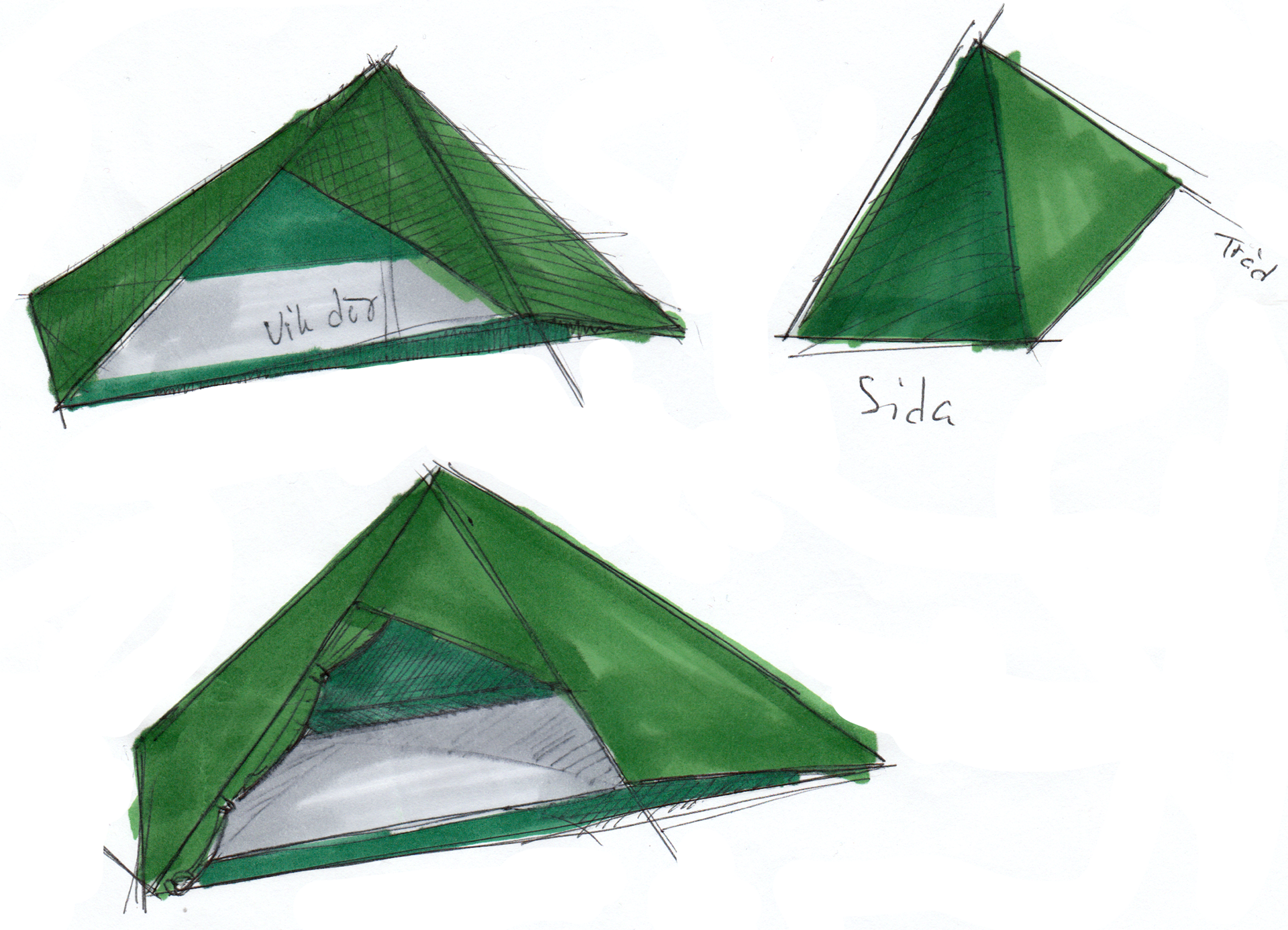
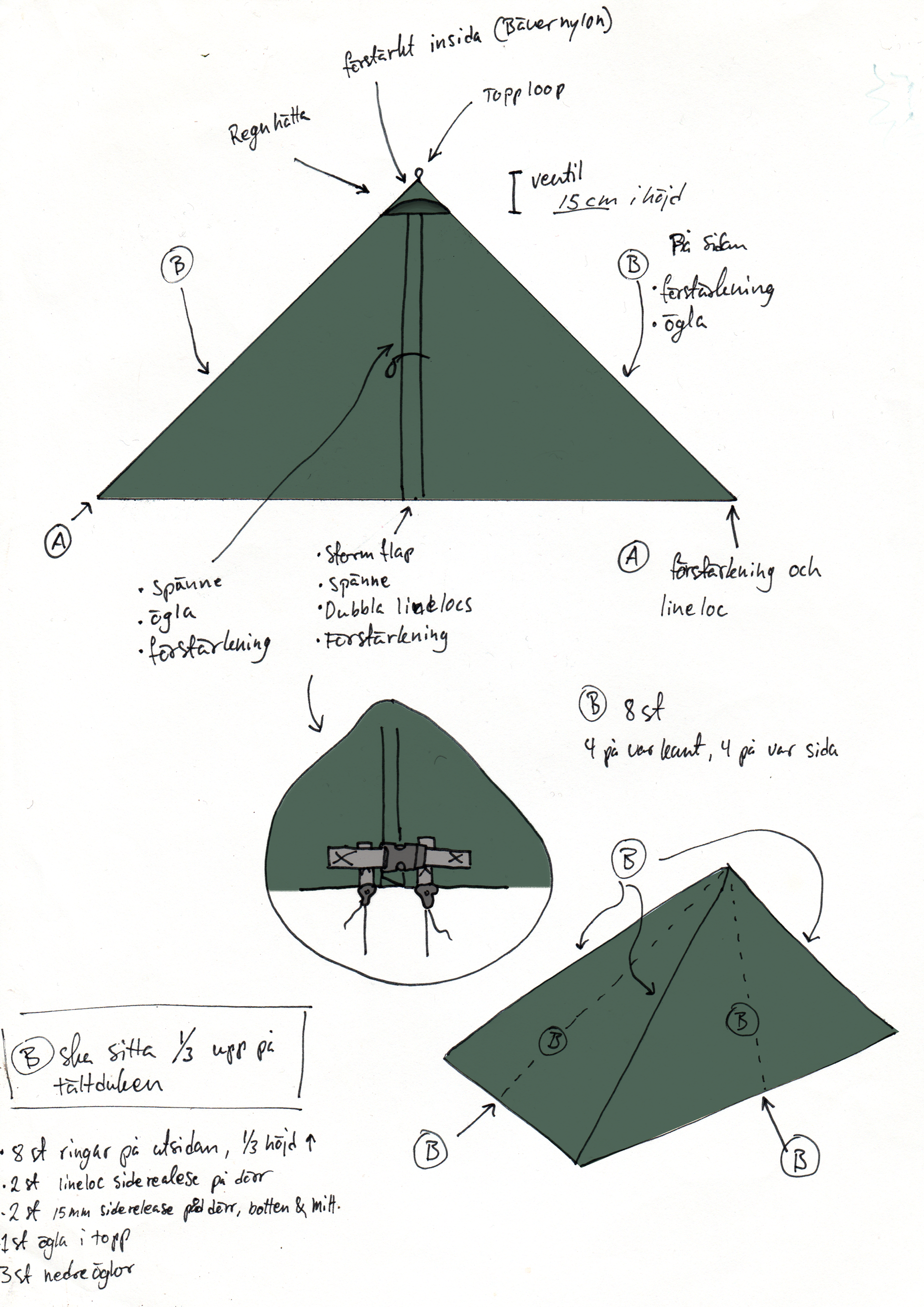
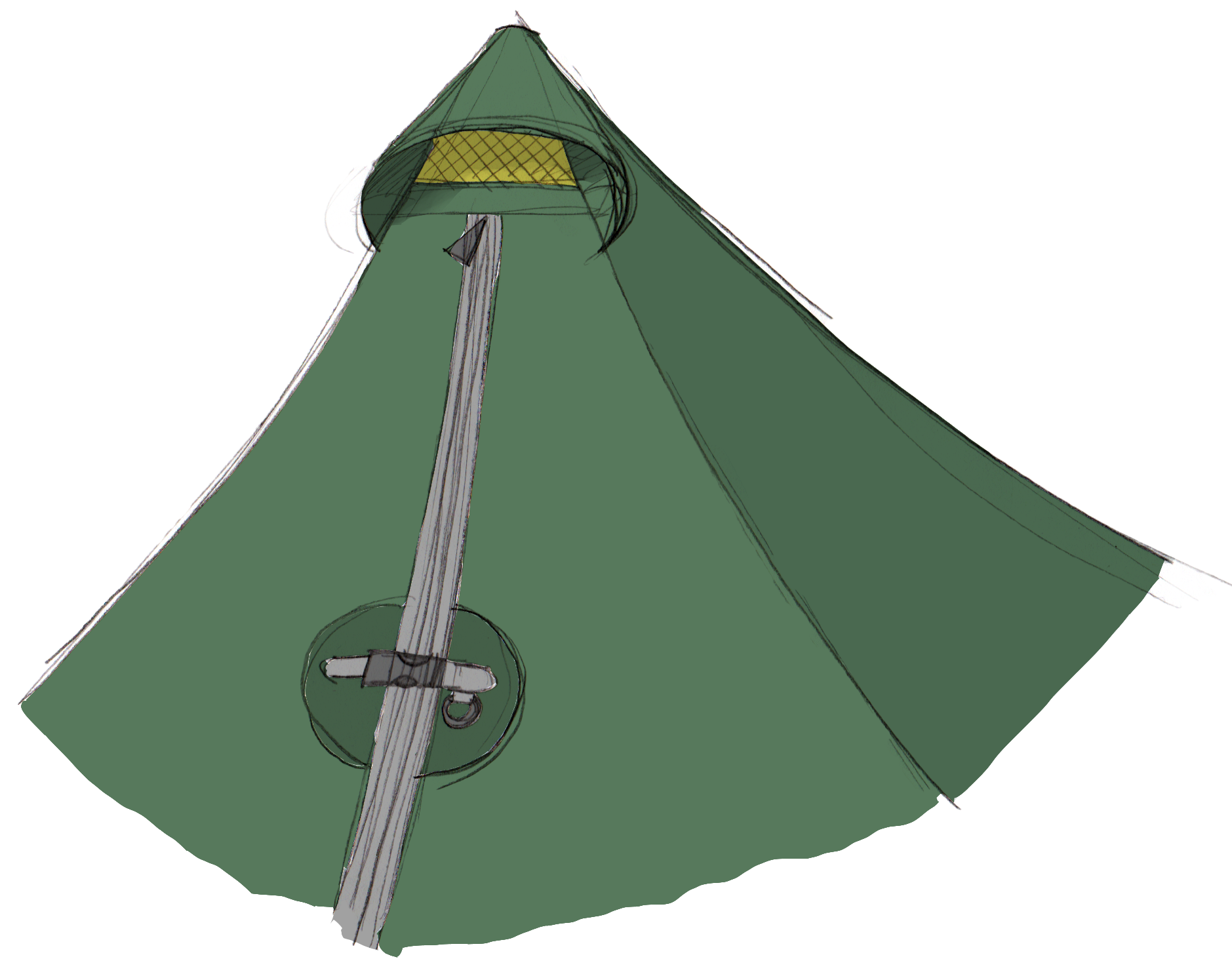
Reinforcement and buckle to relieve stress on the outer fly zipper.
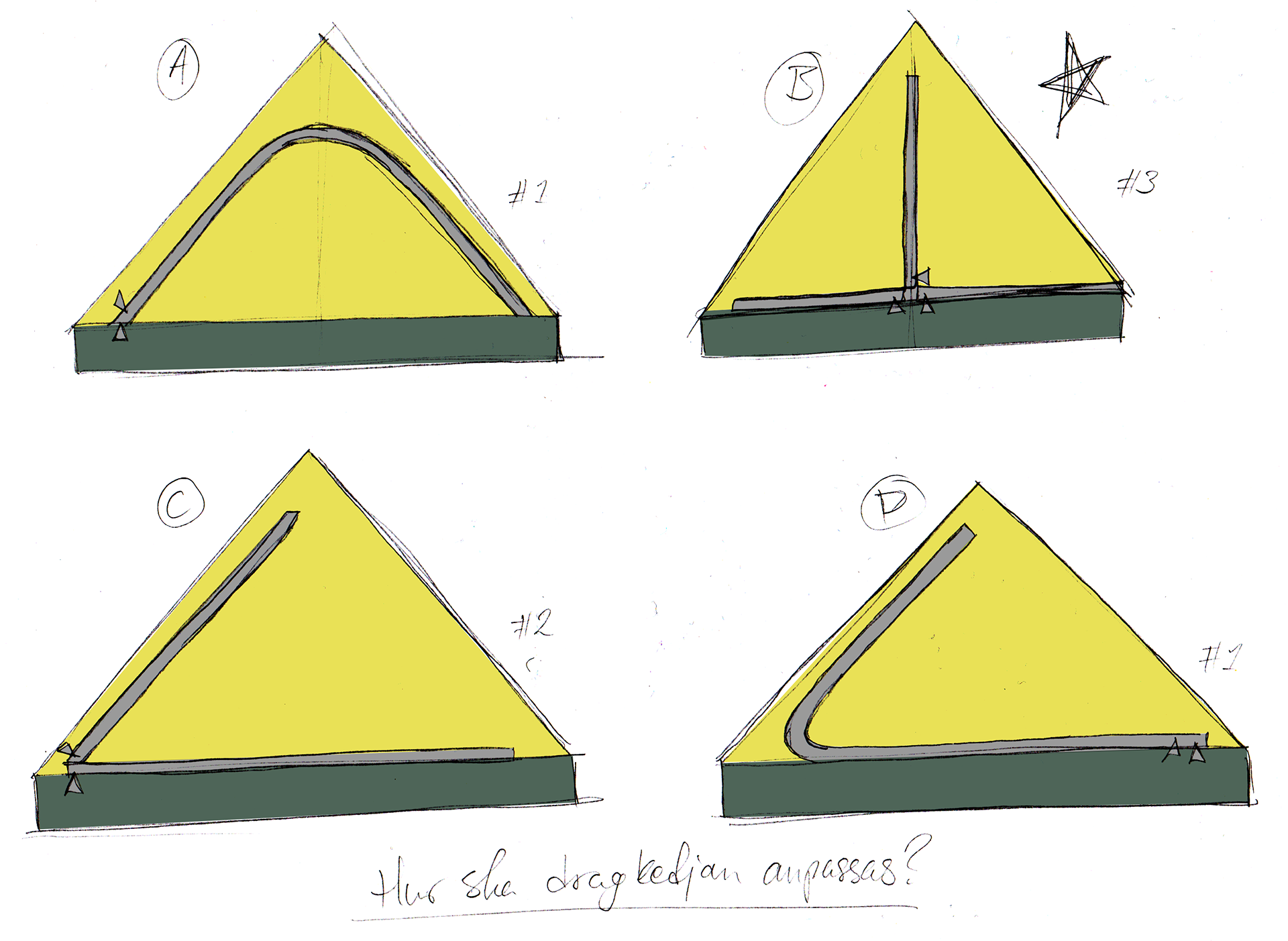
Sketches of how the zipper of the inner tent should be placed to offer the most flexible solution.
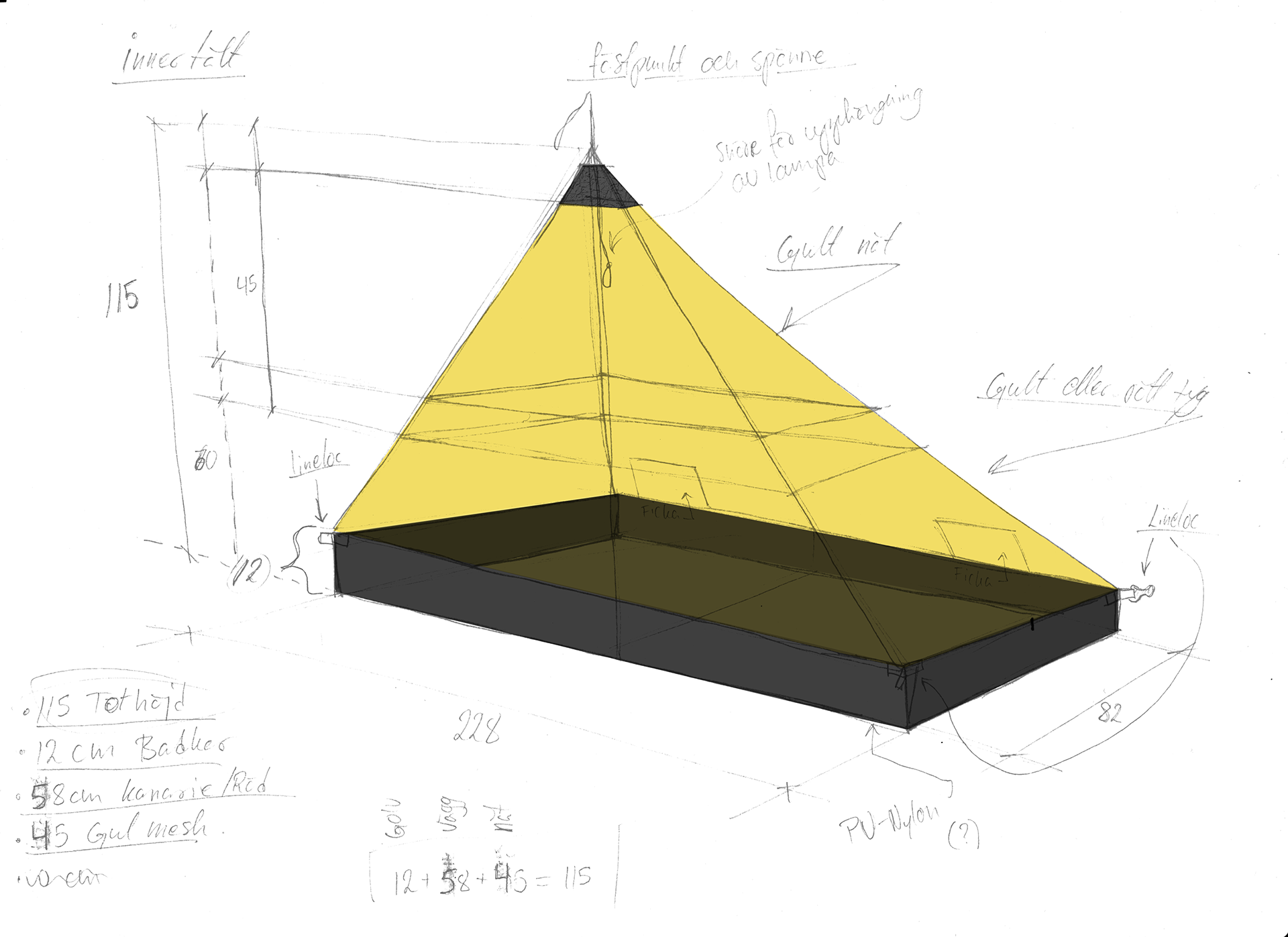
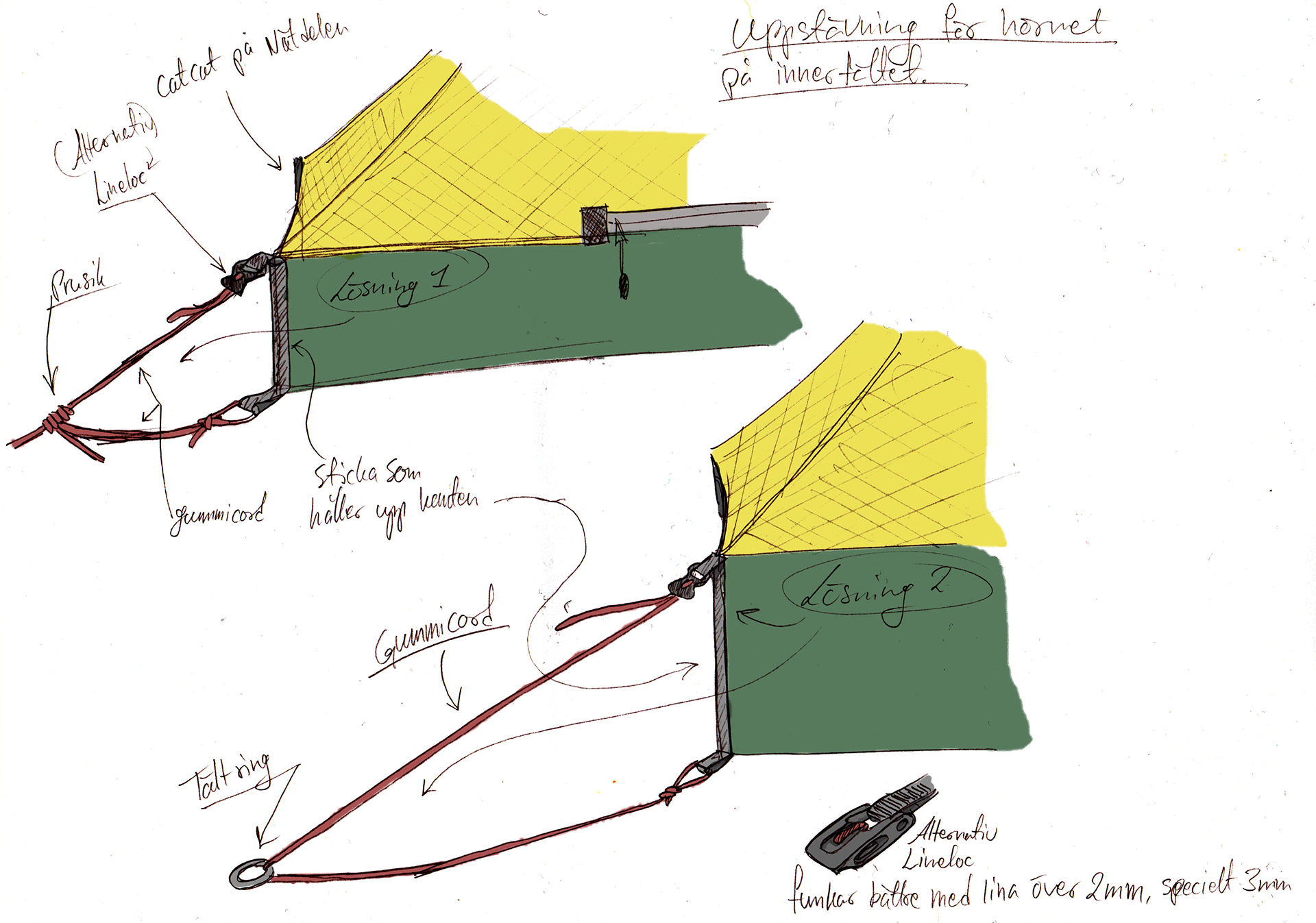
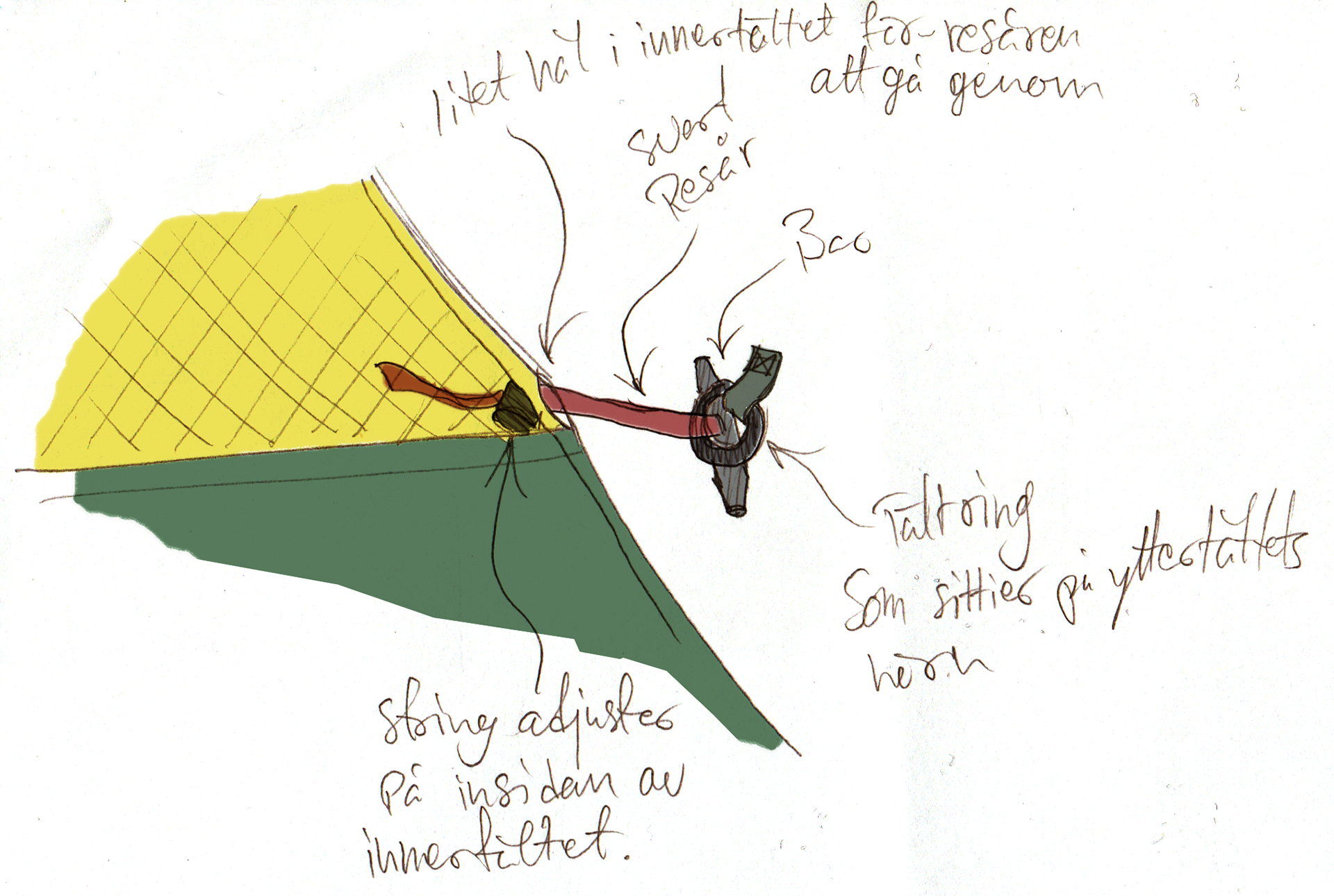
Attachment for the bathtub floor and the net at mid height of the inner tent to the outer fly.
Evaluation of Ideas
The perks of the pyramid shape seemed to outperform the other possible shapes when all the factors of weight, ease of production, pitching and stability are factored in.
The next step would be to define measurements to maximize living space inside the tent. Here I used CAD to test out different concepts for width, depth, height as well as different solutions for the inner tent. With the height that I realized would be required, a trekking-pole extender was needed to extend the pole.
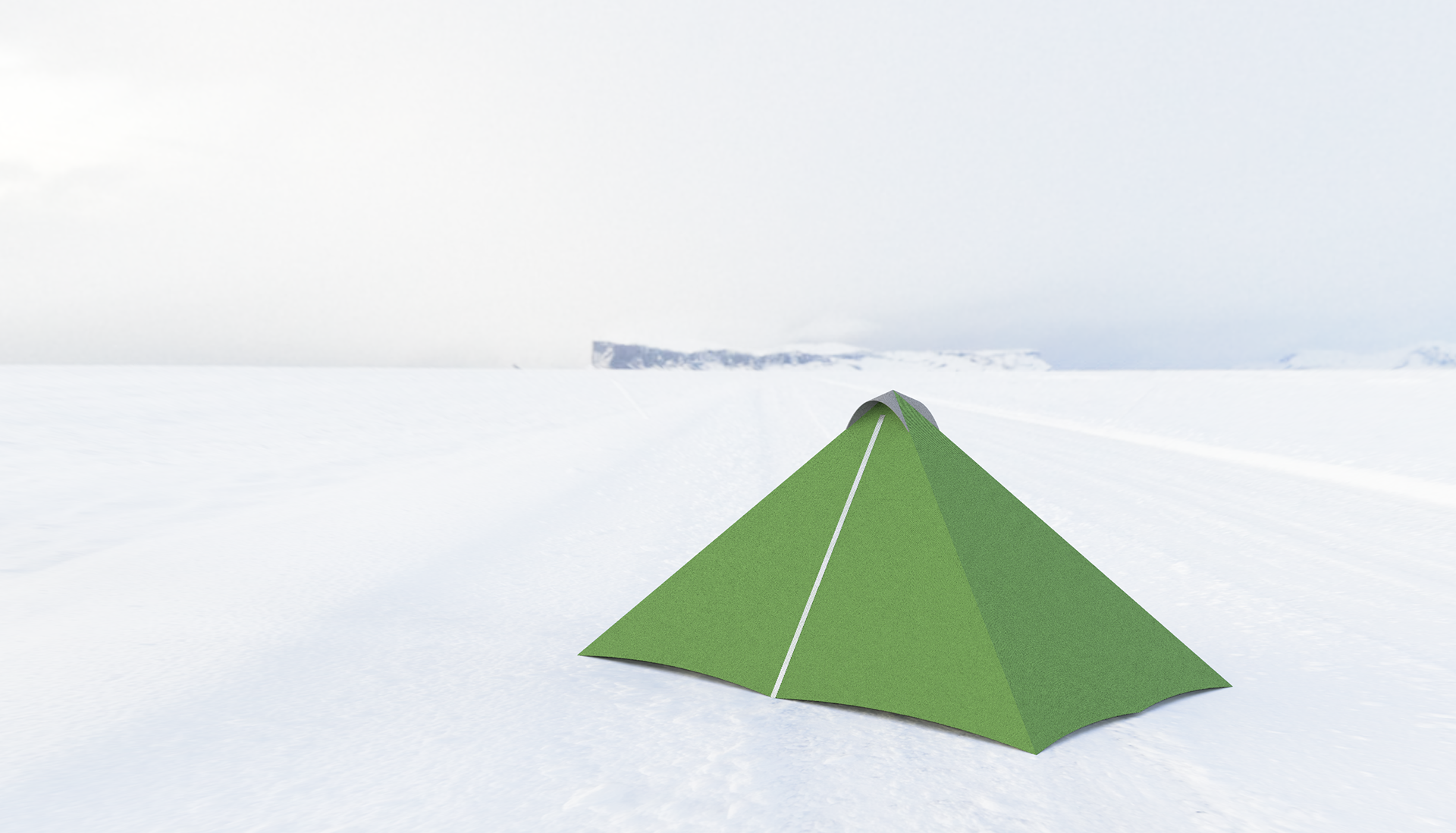
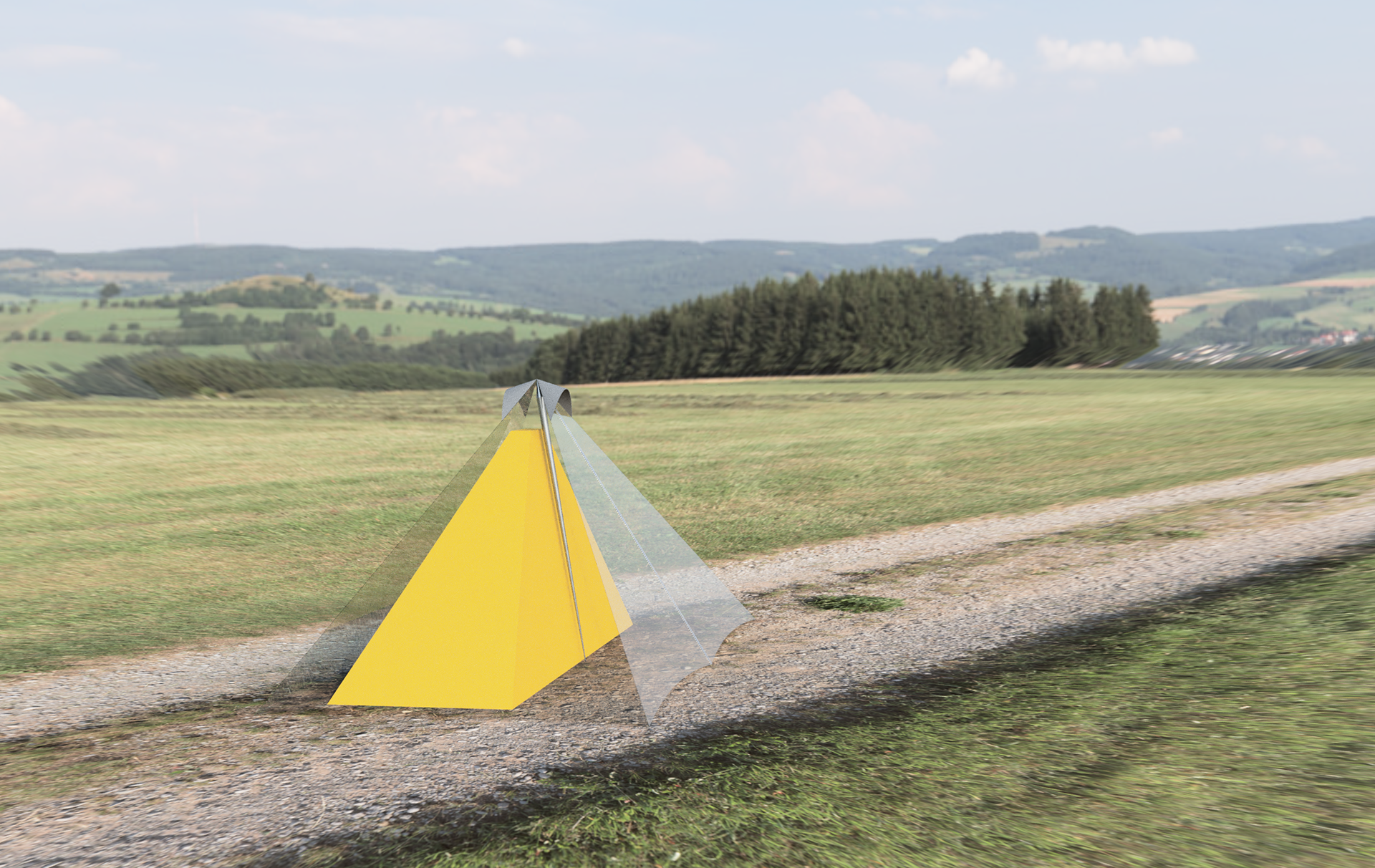
Manufacturing
To create the pattern for the outer tent I first created a model in CAD and transferred these measurement to full-size paper patterns. As the sides of the tent were bigger than the fabric I had to make all sides in multiple parts. To maximize the use of the fabric on hand I chose to split all the sides along the middle. The seams were fully flat-felled to provide the best tear strength and later seam sealed with silicon to be fully waterproof.
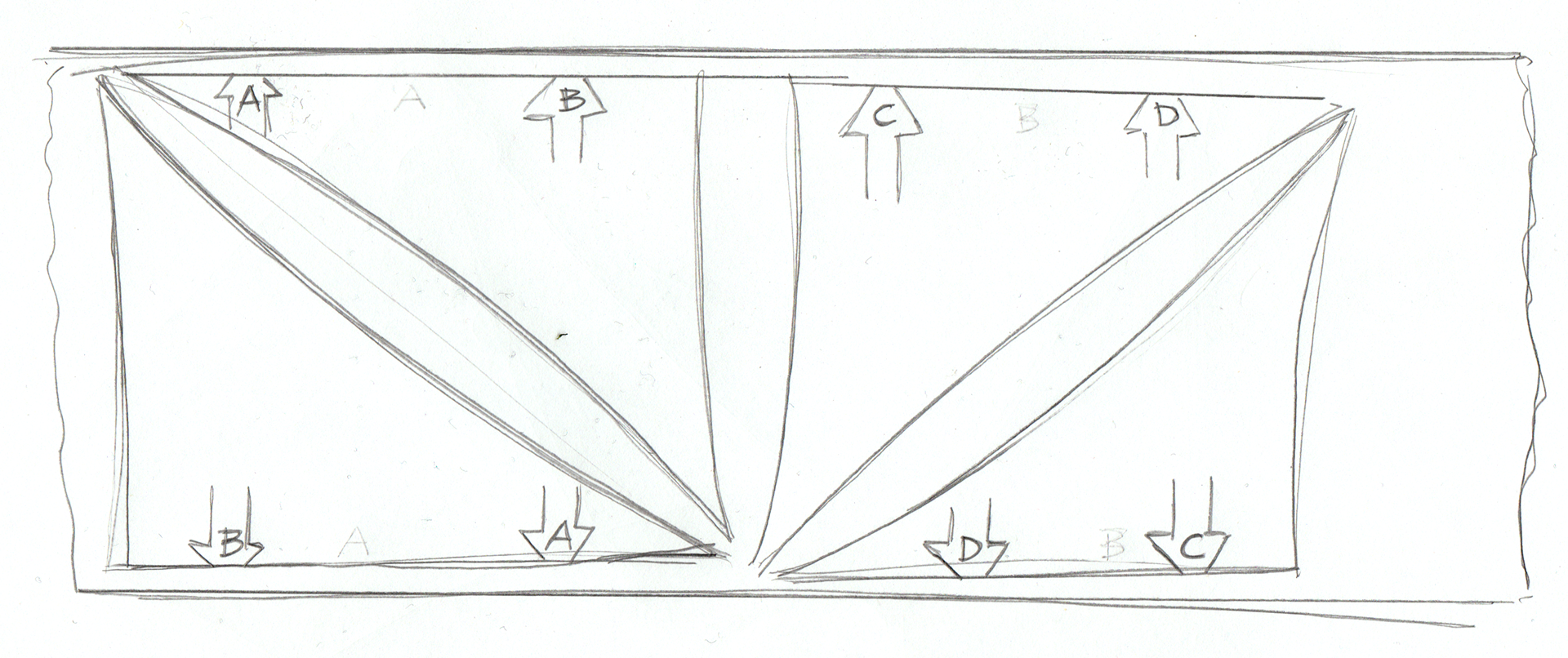
Visualizing the layout of the pattern and the cat-cuts on the outward sides.
Product
The pole extender came to be 30 cm and be made of an aluminium pipe with a champagne cork as a foot. This turned out to be the best solution without using a more expensive but slightly lighter solution in carbon fiber.
It is possible to use two poles with double pole extenders to set up the trekking poles in an A-frame and thereby provide a floor area unobstructed by a pole and more easily house two people.
Using an inner tent that takes up about half of the space inside the outer tent - it is meant to be used by one person and still provide a generous abside for gear and other uses.
To counter the stretch of the Sil-Nylon I used so called ”cat cuts” on all outward edges. The name refers to catenary curves which is the special curves that is created when a string is hanging freely between two points. When the Sil-Nylon is stretched, the curves are stretched out closer to a straight line and forcing the center fabric to also stretch out and therefor prevent sagging.
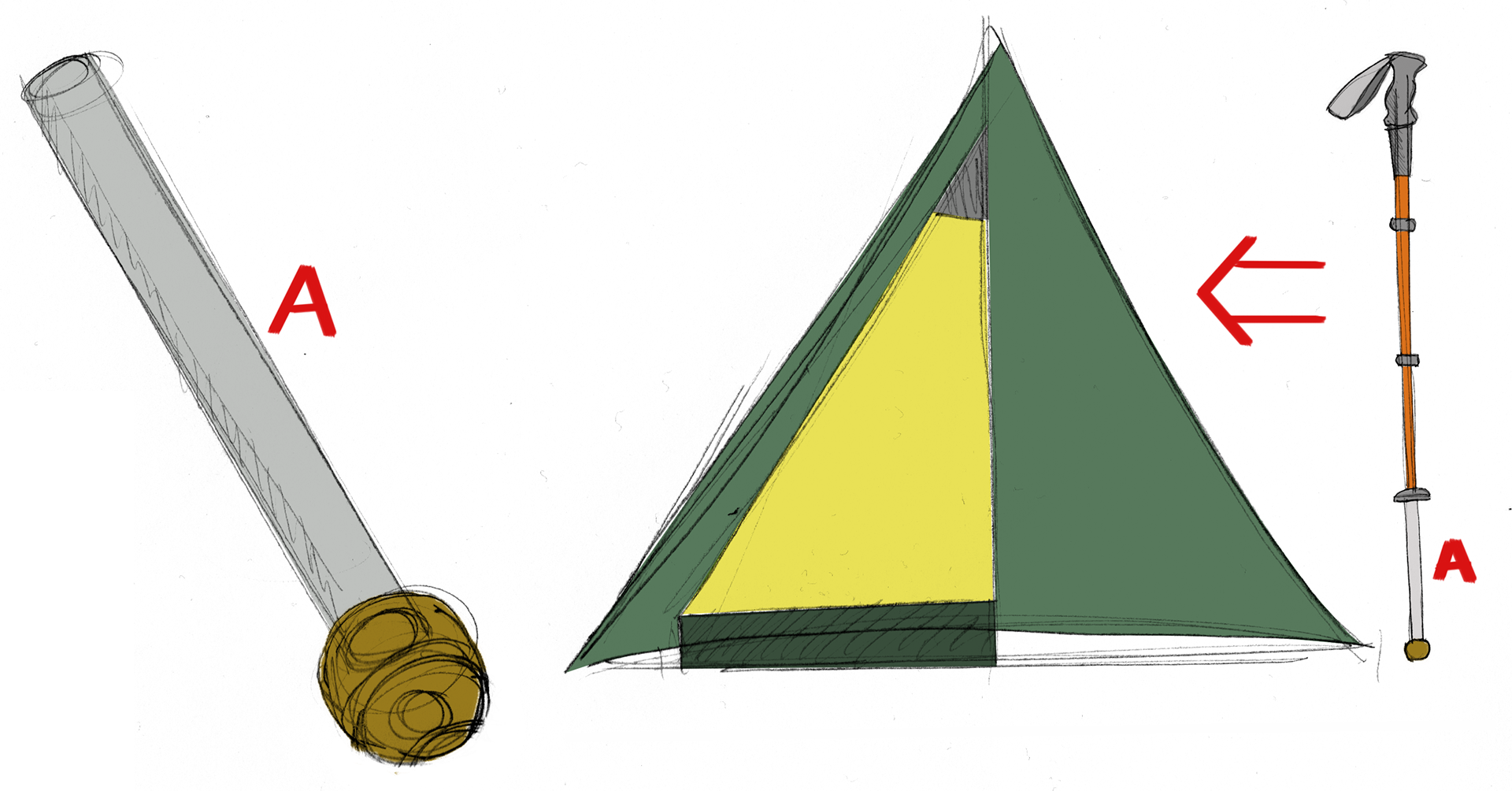
The pole extender that enables the tent to be pitched using only one trekking pole.
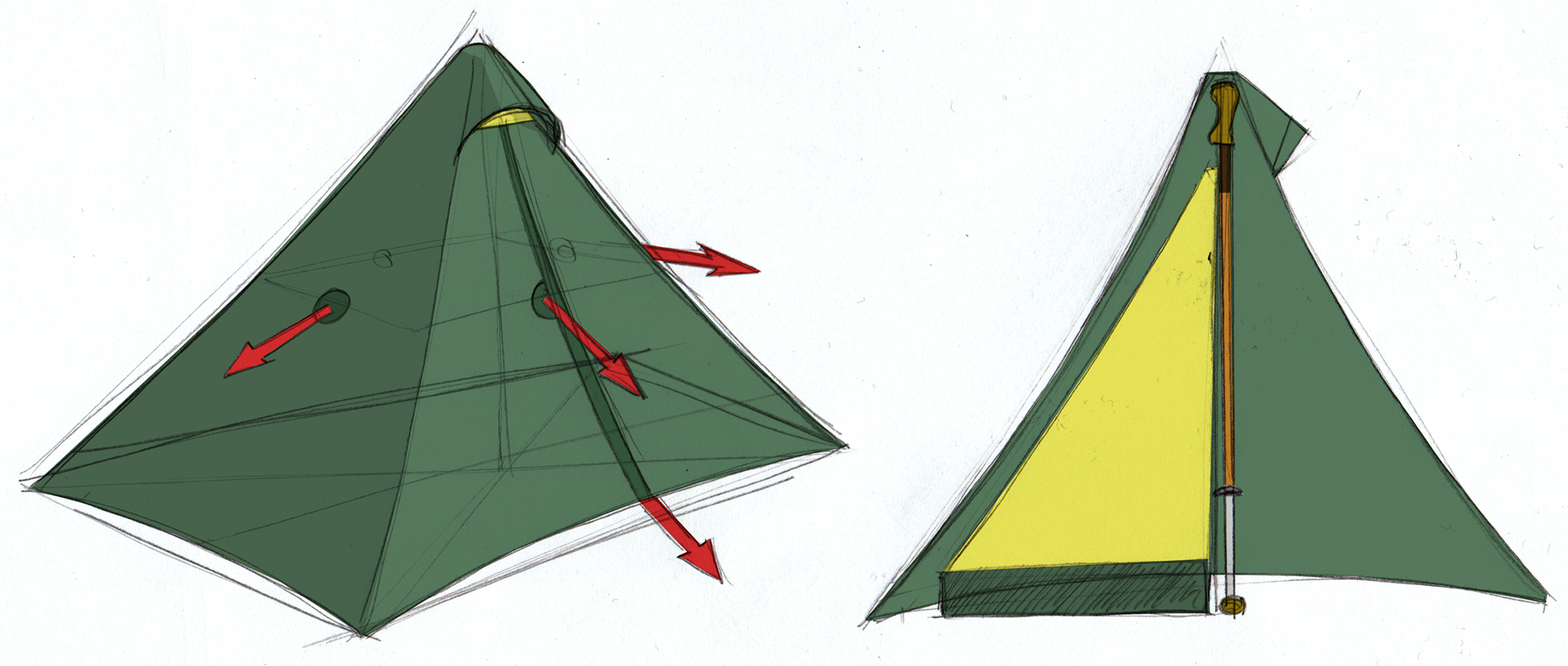
Red arrows showing the connection and pulling of the external guy lines. The right sketch shows the outer fly coupled with the inner for one person, providing a generous abside with room for gear
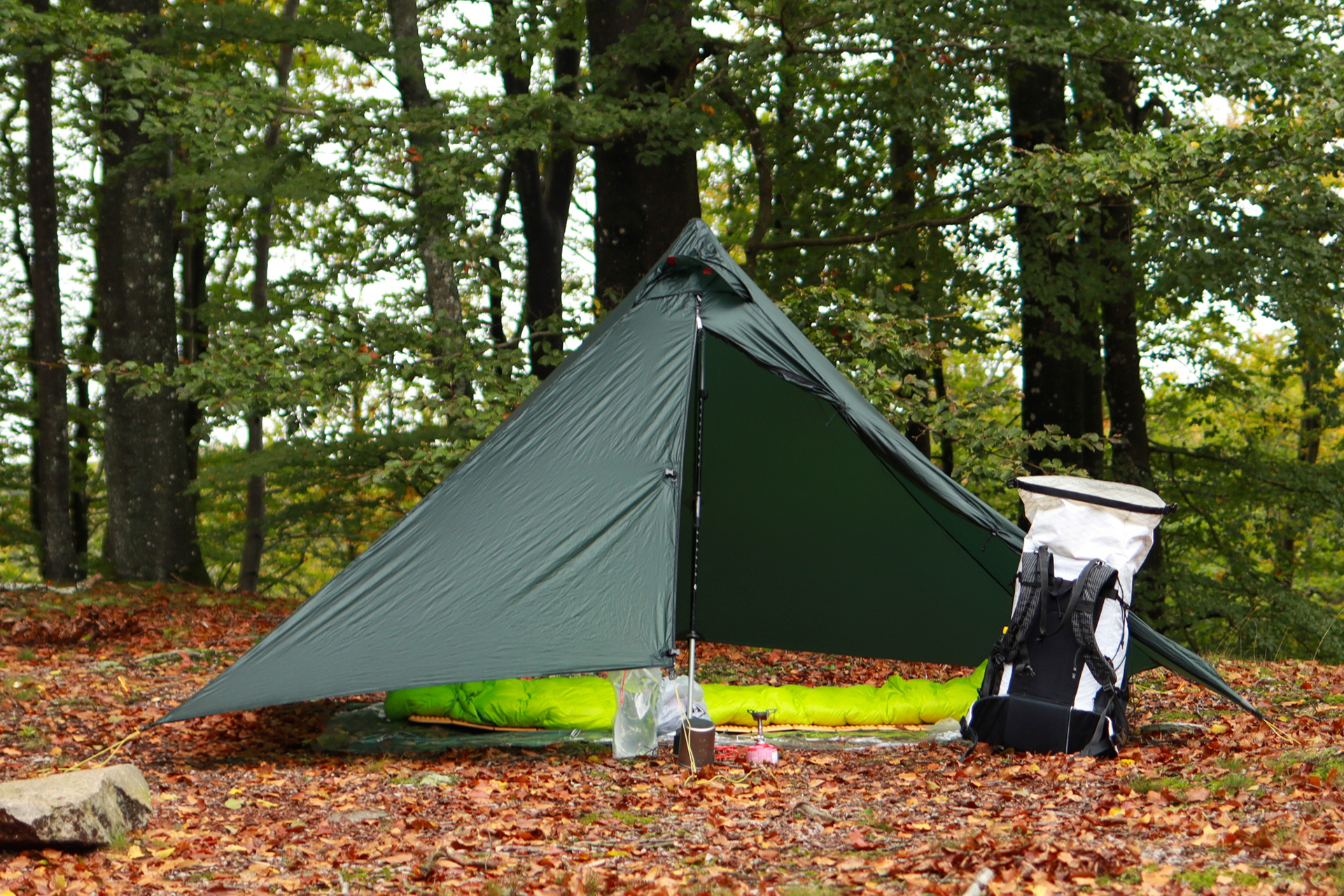
Fall camping and the tent pitched without it's inner tent. The modularity enables lowered carried weight and good adaptability to various needs and adventures
Evaluation of Product
The tent turned out to be great and succeeding in all of the goals that were set up but a refinement of the pattern and production could be needed for better finish.
The concept proved to be capable but the inherent con of the tent is the craftmanship and layout of pattern. The craftsmanship is more or less to be expected with my hobby experience and a simpler sewing machine. What could be most easily improved is the cut of the pattern. The vertical mid split prevents the walls to stretch from the mid center and out and this increases the amount of bunching and creasing. The walls should instead be cut with a seam and smaller extra panel at the top of the peak, reducing the amount of seams.
The tent is provides great sturdiness as the main pole is being stabilized from all directions. The top vent provides something that can closest be resembled to a chimney effect, taking fresh air from the sides as warmer air goes exits at the top.
The pitching is quick and easy as long as the ground pegs can be securely fastened to the ground. The weight of the outer fly turned out to be 430g, and a total of 880g not including ground stakes.
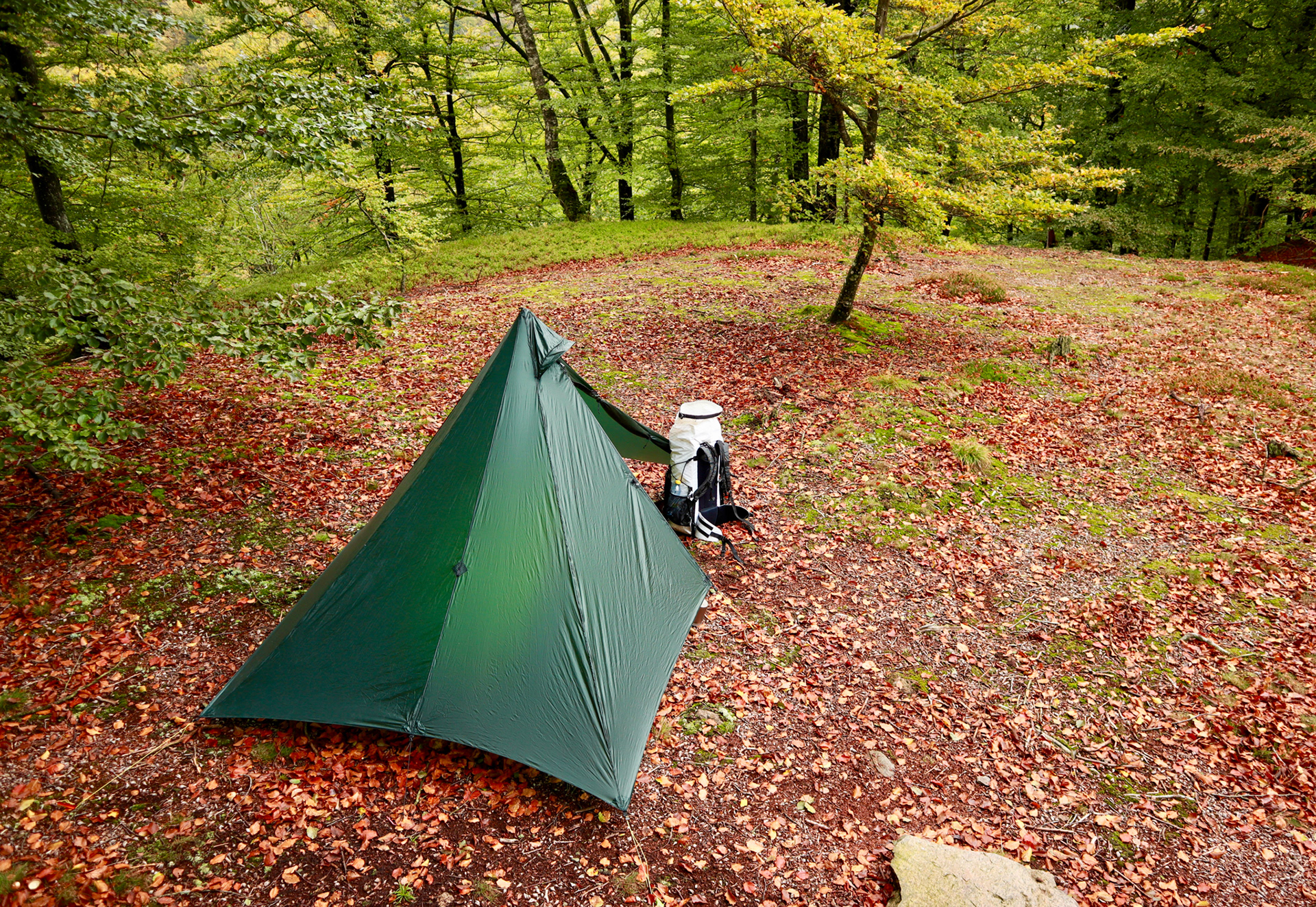
While the weight is not high compared to what it offers in livable space and the possibility to sleep two in it, it could definitely be lighter. As it is mainly fabric that would be the obvious place to save weight by going with a lighter fabric. The fabric it is made of is relatively thick, especially for a lightweight tent as I would believe this to be the fabric Hilleberg uses for either their Red or Black-label tents. I could not go with the thinnest Sil-Nylon that I could find (10D) as it was too thin and slippery for me to sew flat-felled seams in with the gear that I had access to.
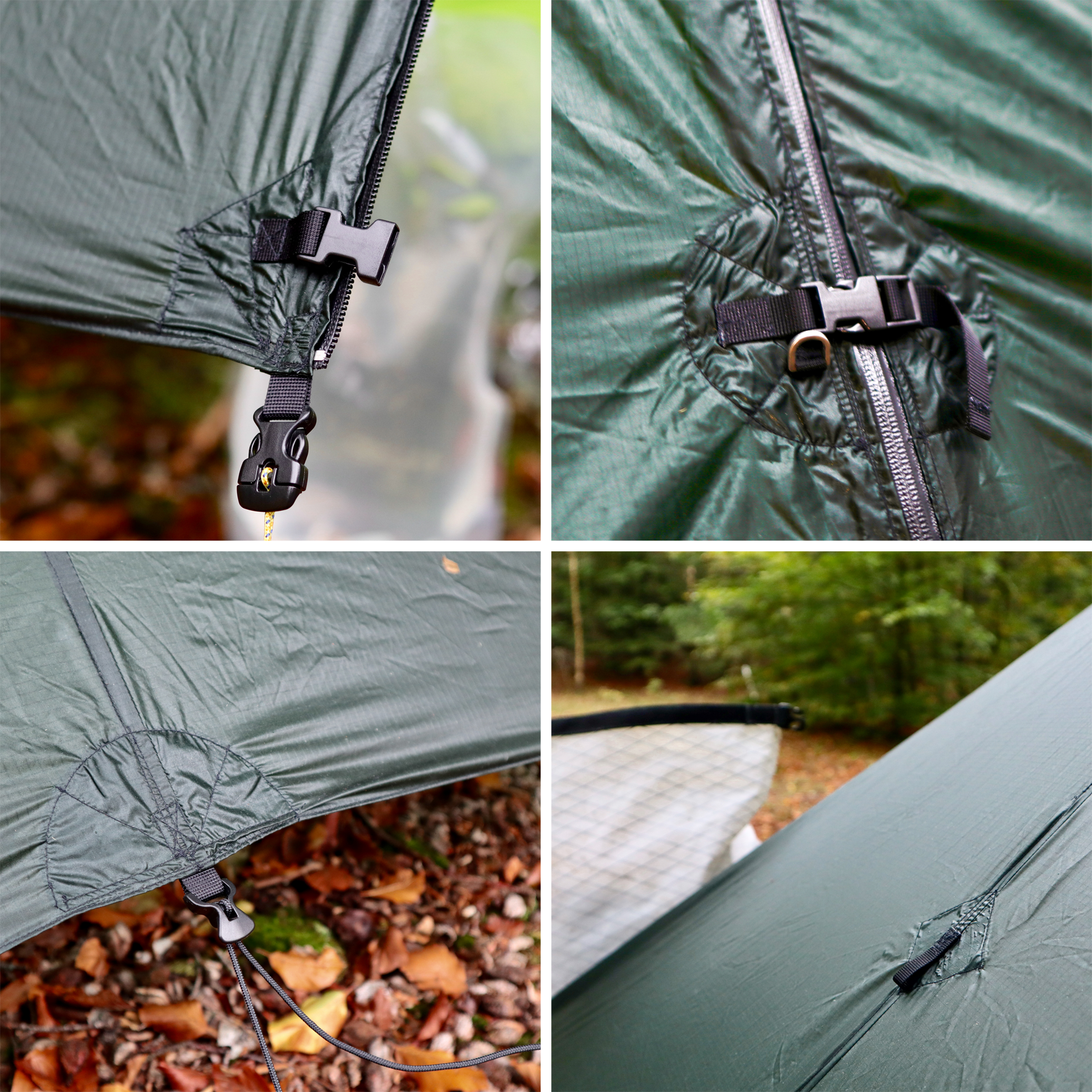
Different points of tie-out and reinforcement. The two buckles over the zipper are meant to relieve the zipper during opening and closing if the tent is pitched tight. The ability to add mid-height guy lines is there to to aid if heavy wind is expected. The same goes for the center placed tie-down points on either side. They help with keeping the tent firmly lowered to the ground.
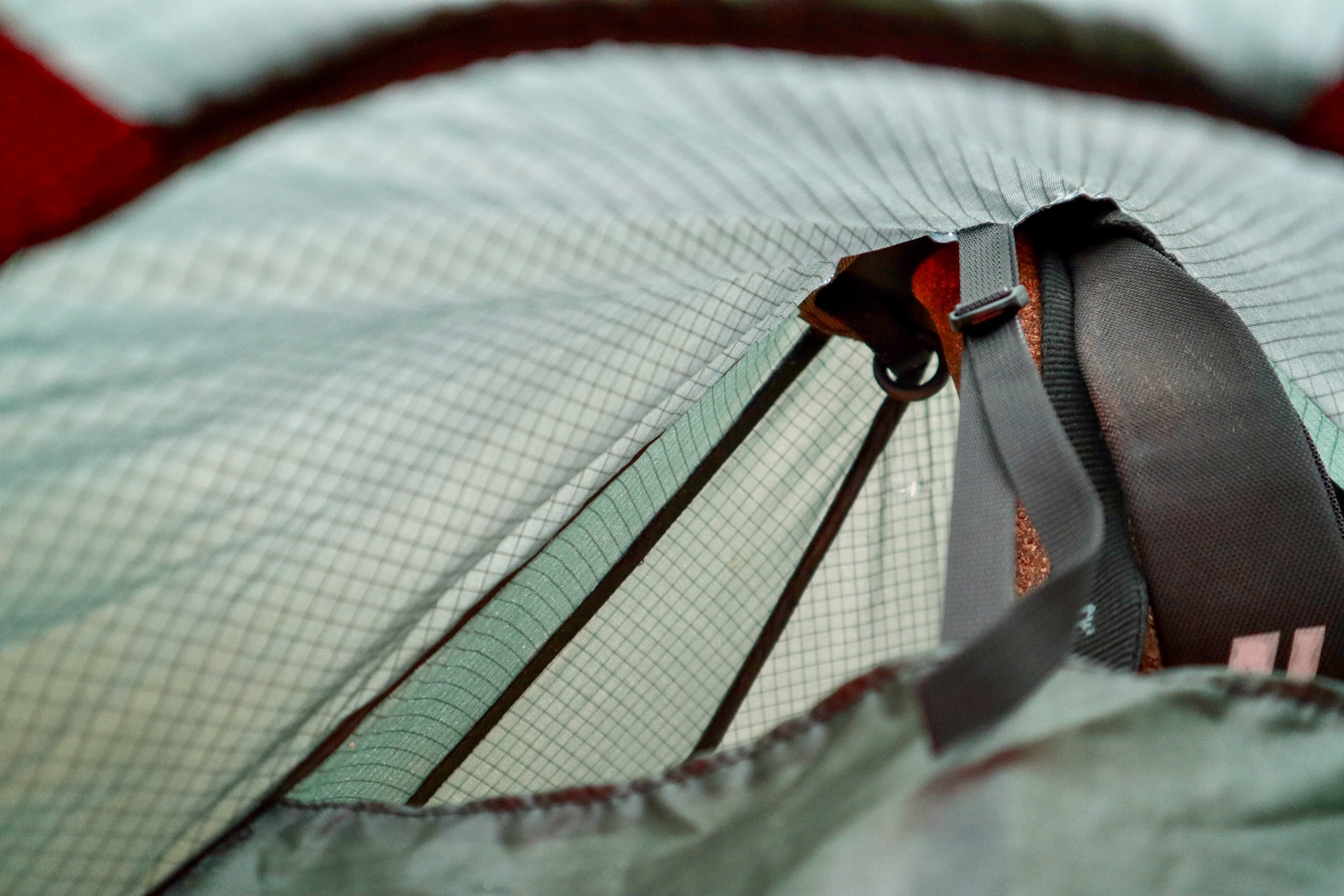
A thin adjustable 10mm webbing anchors the top of the zipper to the top of the tent. This mitigates the lowered structural stability created by having no fabric where the vent is. Without this it would not be possible to open the doors without destabilizing the front panels. An essential but easily overlooked part.